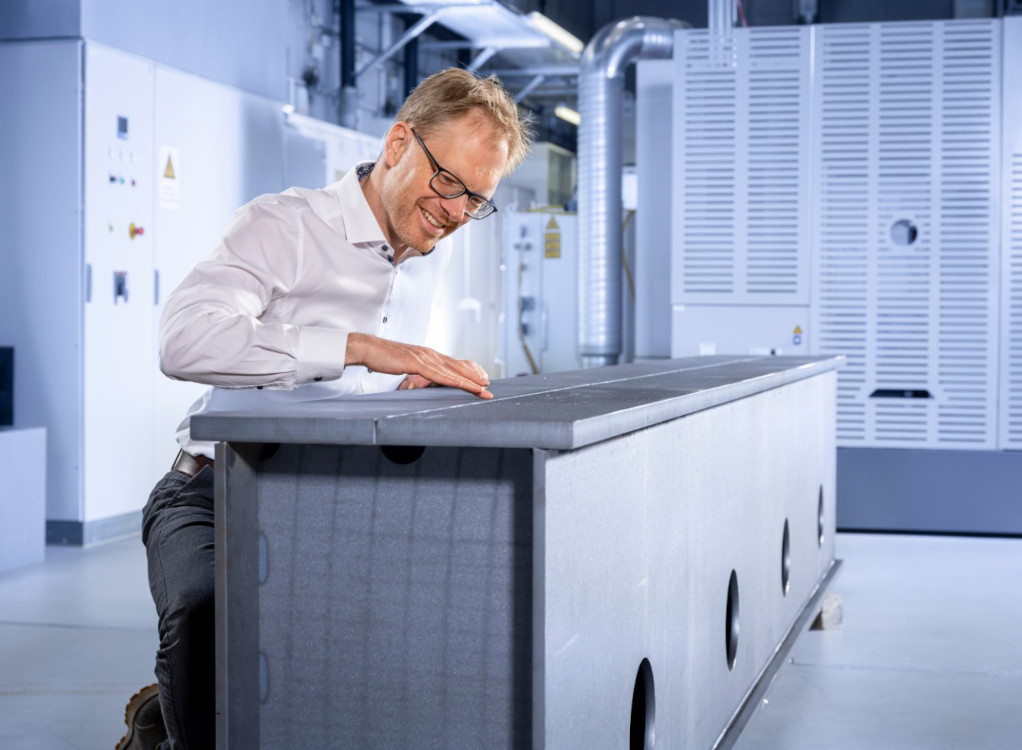
11 Apr Laserschweißen soll Stahlbau revolutionieren
Ein für den Stahlbau angepasster Laserschweißprozess bietet eine schonendere Bearbeitung hochfester Werkstoffe bei deutlich verringerten Energieaufwendungen und Kosten und stark erhöhter Prozessgeschwindigkeit. Verglichen mit konventionellen Fügeverfahren lässt sich der Energieeintrag ins Bauteil um bis zu 80 % reduzieren. Das anschließende Richten des Bauteils entfällt ganz.
Egal ob Containerschiffe, Schienenfahrzeuge, Brücken oder Windkrafttürme, in allen diesen Konstruktionen können mehrere 100 Meter Schweißnaht vorhanden sein. Üblicherweise kommen dafür konventionelle industrielle Verfahren wie das Metall-Aktivgas-Schweißen oder das Unterpulverschweißen zum Einsatz. Das Problem dabei: Durch die geringe Intensität des Lichtbogens fließt ein Großteil der aufgewendeten Energie nicht in den gewünschten Schweißprozess, sondern geht in Form von Wärme in das Bauteil verloren. Der Energiebedarf für die Nachbehandlung der Schweißnaht liegt vielfach in ähnlichen Größenordnungen wie derjenige für den eigentlichen Schweißprozess.
Neuer Ansatz mit marktüblichen Lasern
Ein Forscherteam um Dr. Dirk Dittrich vom Fraunhofer-Institut für Werkstoff- und Strahltechnik IWS hat im Projekt ‚VE-MES – Energieeffizientes und verzugsarmes Laser-Mehrlagen-Engspalt-Schweißen‘ gemeinsam mit Industriepartnern eine energieeffiziente Alternative entwickelt. Das Laser-Mehrlagen-Engspalt-Schweißen (Laser-MES) bringt einen marktüblichen Hochleistungslaser zum Einsatz und besticht im Vergleich zu herkömmlichen Methoden durch verringerte Lagenanzahl und drastisch reduziertes Nahtvolumen. Daraus ergeben sich die entscheidenden Vorteile dieses Schweißverfahrens. „Wir können den Energieeintrag in das Bauteil beim Schweißen – je nach Komponente – um bis zu 80 % und den Zusatzwerkstoffverbrauch um bis zu 85 % im Vergleich zu herkömmlichen Lichtbogenverfahren senken“, unterstreicht Dittrich. „Zudem war am betrachteten Bauteil kein Richtprozess mehr erforderlich. Dadurch reduzieren wir Fertigungszeit und -kosten, können auch hochfeste Stahlwerkstoffe verarbeiten und verbessern die CO2-Bilanz der gesamten Fertigungskette deutlich.“ Denn die hohe Intensität des Laserstrahls garantiert einen sehr lokalen Energieeintrag an der Schweißstelle, wohingegen die umliegenden Bauteilbereiche vergleichsweise kalt bleiben. „Die Schweißzeit reduziert sich zudem um 50 bis 70 %“, so Dittrich weiter. Außerdem sind die Schweißnähte deutlich schlanker und nahezu flankenparallel, während sie bei konventionellen Schweißprozessen V-förmig ausgeführt sind. „Den Laser in den Stahlbau einzuführen, würde für die mittelständische Industrie in Deutschland ein Alleinstellungsmerkmal darstellen und ihre Marktposition im internationalen Wettbewerb stärken“, ist Dittrich überzeugt.
Prinzip des Laser-Mehrlagen-Engspalt-Schweißens
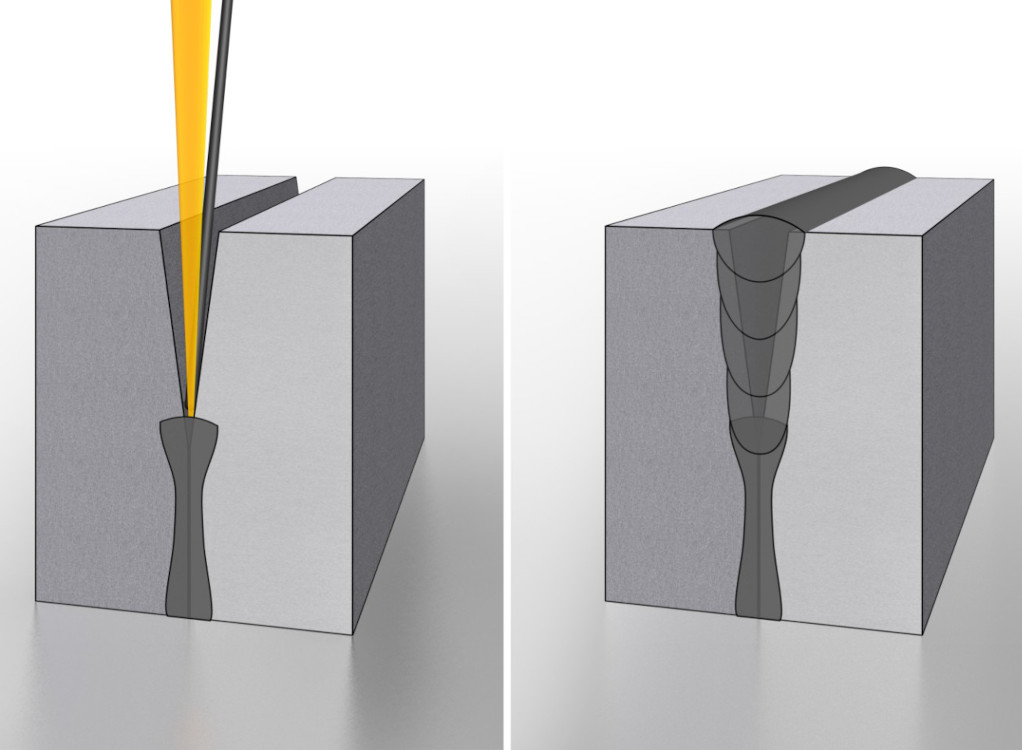
Der Laserstrahl wird in die Fuge zwischen den beiden zu verschweißenden Blechkanten positioniert, und gleichzeitig wird davor ein Schweißzusatzwerkstoff hinzugefügt. Bild: Fraunhofer IWS
Der Laser wird in die Fuge zwischen den beiden zu verschweißenden Blechkanten positioniert, während ein Schweißzusatzwerkstoff hinzugefügt wird. Die Energie des Laserstrahls schmilzt die Flanke der Werkstücke auf, ebenso wie den Zusatzwerkstoff aus dem Draht, der das Volumen zwischen den beiden Stücken auffüllt und eine qualitativ hochwertige Schweißnaht erzeugt. Das Verfahren ermöglicht das Schweißen typischer Stoßkonfigurationen im Stahlbau. Die Blechkanten sind plasmageschnitten, und die Fügestelle weist zum Teil Spalte von bis zu zwei Millimetern Breite auf, die der Laserschweißprozess sicher überbrückt. Sowohl beim Schweißen eines Stegblechs (T-Stoß) als auch beim Schweißen des Stumpfstoßes gewährleistet das Verfahren einen Vollanschluss – eine Verbindung der beiden Teilstücke über die gesamte Kontaktfläche. Beim konventionellen Stahlbau wird dies verfahrensbedingt nicht immer zu 100 % erreicht, insbesondere beim T-Stoß bestehen technologische Grenzen.
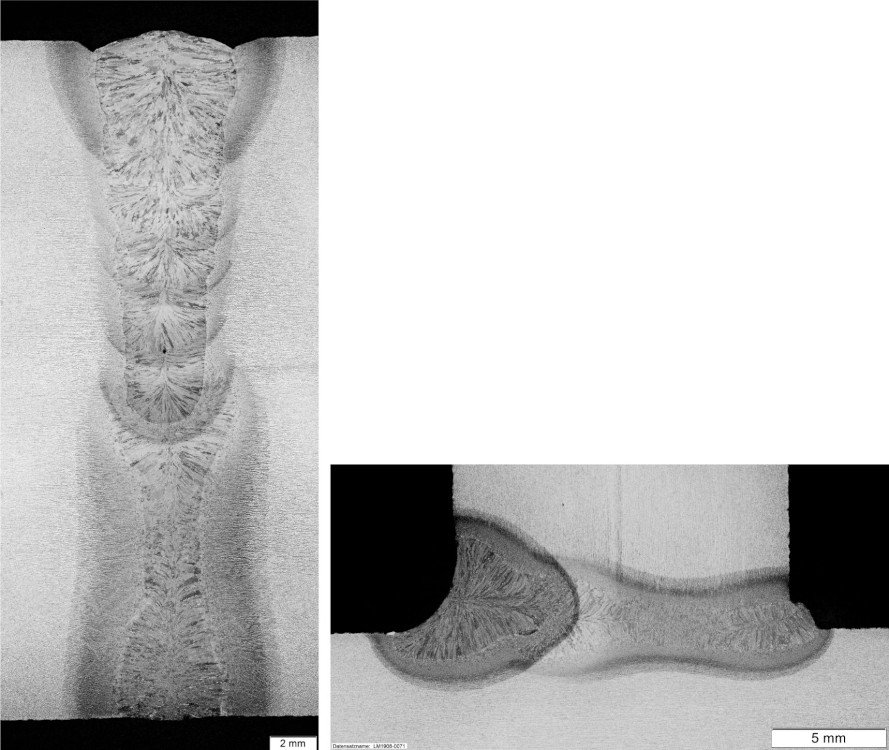
Die Querschliffe einer per Laser-MES erzeugten Stumpfstoßverbindung und einer T-Stoßverbindung zeigen die Nahtqualitäten, die sich mit deutlich reduziertem Kosten- und Ressourceneinsatz herstellen lassen. Bild: Fraunhofer IWS
Stahlträger für den Hallenkranbau
Die Forschenden des Fraunhofer IWS demonstrierten die Leistungsfähigkeit ihrer Entwicklung anhand eines Praxisbeispiels aus dem Hallenkranbau. Sie brachten die neue Schweißtechnologie mit einer speziellen Systemtechnik und einem integrierten Strahlschutzkonzept zum Einsatz. Die Konstruktion des experimentell aufgebauten, vier Meter langen Rechteckprofils eines Hallenkran-Segments entsprach den Design- und Fertigungsrichtlinien vergleichbarer, konventionell hergestellter Bauteile. Erzeugt wurden anwendungstypische Schweißnähte: Ein Stumpfstoß an 30-Millimeter-Blechen und ein vollangeschlossener T-Stoß (15-Millimeter-Blech). Für einen Meter Schweißnaht ließen sich die Kosten für eine Blechdicke von 30 Millimetern gegenüber dem Unterpulverschweißen inklusive des nachträglichen Richtprozesses um 50 % senken. Für Blechdicken unter 20 Millimetern, bei der herkömmlicherweise auch Metall-Aktiv-Gas-Schweißverfahren eingesetzt werden, liegt die potenzielle Kostenersparnis mit bis zu 80 % noch höher. Allein die Kostenersparnisse bezüglich der Schweißzusatzwerkstoffe kann in größeren Unternehmen bei mehr als 100 000 Euro pro Jahr liegen. Zusätzlich bieten die eingesetzten Laserstrahlquellen aufgrund ihres hohen Wirkungsgrades (ungefähr 50 %) und der guten Prozesseffizienz (Reduktion des Energieeintrages um 80 %) großes Potenzial, die steigenden Energiekosten einzudämmen. Mit diesem Nachweis der Praxistauglichkeit lässt sich der Lösungsansatz nun auch auf andere Anwendungen übertragen.
Quelle und Bild: www.iws.fraunhofer.de