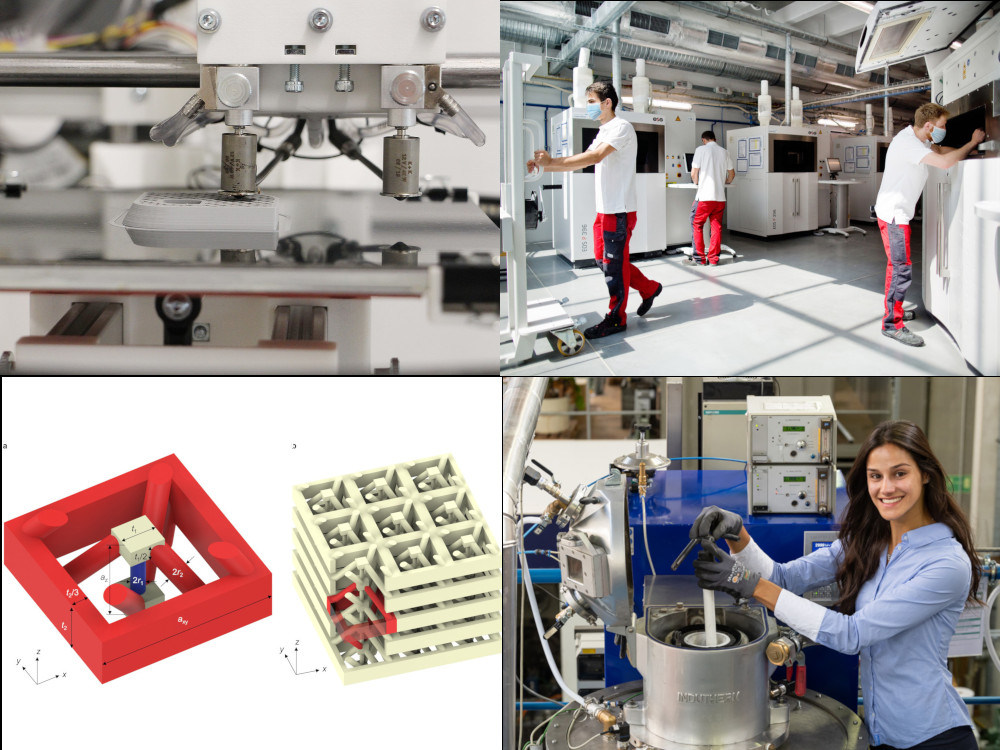
14 Jun Review of the week
Nowadays, many different additive manufacturing technologies already exist, which are also summarised under the term 3-D printing. More and more materials are therefore also suitable for use in the 3-D printer. Among the most common are metals, alloys, polymers and ceramics.
What exactly is 3-D printing?
In traditional manufacturing, many product components are made by milling or grinding a base material to obtain the final geometry. This is a subtractive process. Another approach is shaping processes. These include mechanically shaping the raw material into the final product or pouring viscous or liquid material into prefabricated moulds of the final product. Additive manufacturing, or 3D printing, on the other hand, produces the final product by building up the material layer by layer. This requires a computer, 3-D modelling software, a printing machine and the layered material.
In many cases, the raw material is a powder, for example in selective laser melting. Here, a thin layer of powder is applied in a bed. The shape of the object is written into the powder layer by layer by laser by melting the material with high spatial resolution. Various melting techniques can be used in this process step. The melted powder becomes solid in the heated areas and thus becomes part of the final component. The process is repeated layer by layer until the 3-D object is built up. Powder as a base material is not the only approach. Another common technology is material extrusion. Here, the material, for example a polymer, is forced through a heated nozzle. The molten material also builds up layer by layer and hardens to form the object. Some products are already usable after printing, others require post-processing such as polishing or a final sintering process to achieve the specific material properties of the object.
However, welding of 3D-printed components by laser could not be implemented so far. Read why this is so and how a solution is to be developed in a joint project in our news item ‘Joining 3-D-printed plastic components with lasers’. The project is also still looking for industrial project partners; in particular specialists in artificial intelligence and additive manufacturing.
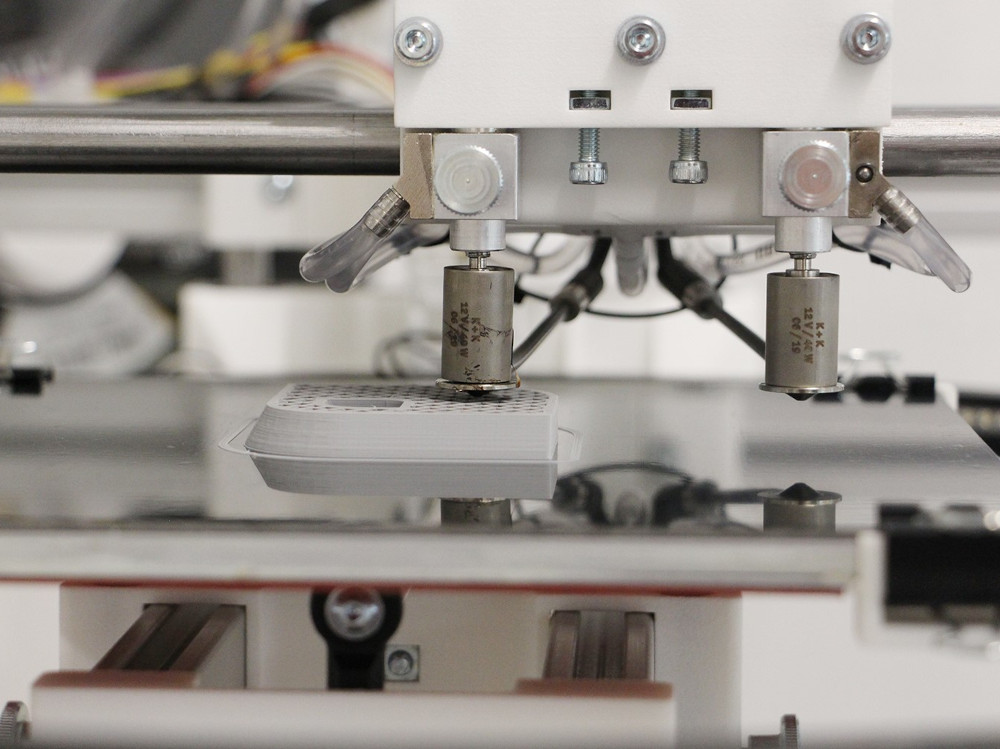
Fused Deposition Modeling (FDM): In this 3D printing process, plastic components are built up layer by layer.
Components for modern aircraft generally have to meet particularly high requirements. Here, too, 3D printing is playing an increasingly important role. You can read about which aircraft components the two companies Materialise and EOS are now supplying to the aircraft manufacturer Airbus in our news item ‘Airbus certifies 3D-printed aircraft components‘.
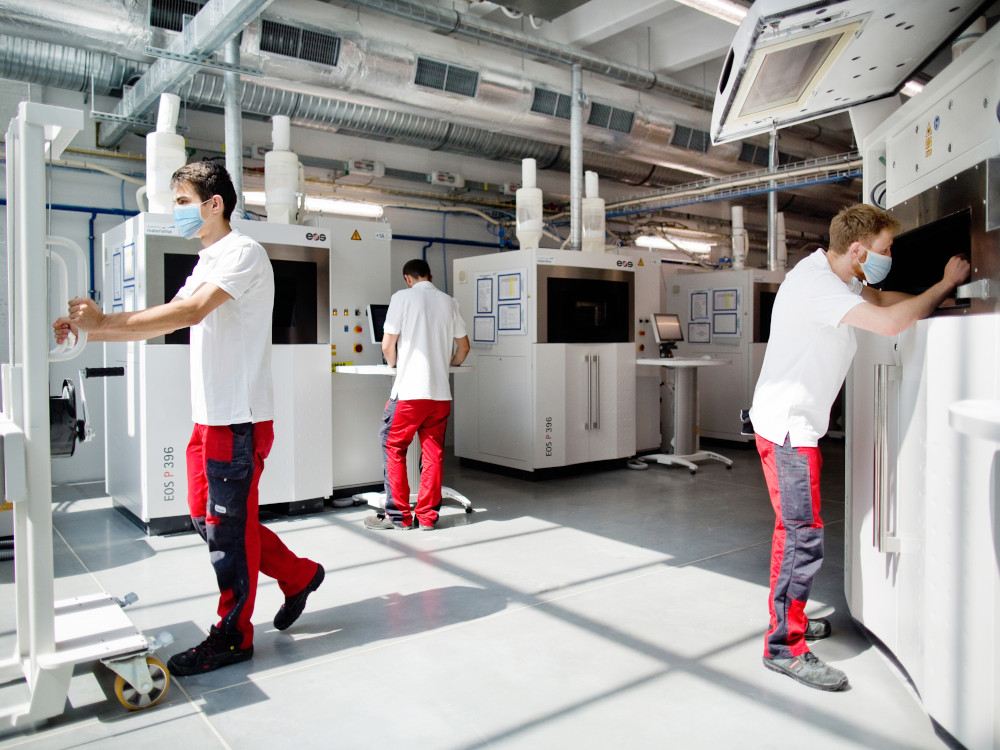
Materialise production hall with EOS systems for 3D printing. Source: Materialise
Materials scientists and physicists are now looking to use 3D printing to produce particularly exotic materials. Read our news story ‘Metamaterial from 3D printer makes sound waves run backwards’ to find out how nature is to be outwitted using metamaterials from 3D printers. A wish that researchers may soon make a reality.
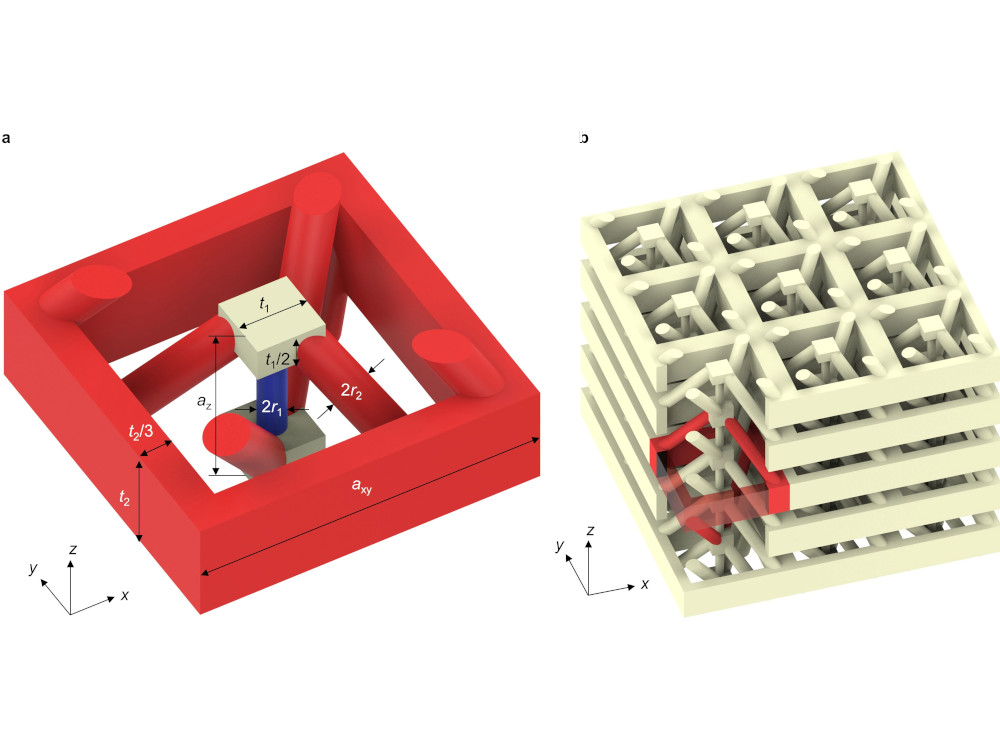
Quelle: Yi Chen, KIT
Leibniz-IWT live
Would you like to learn more about 3-printing? The Leibniz Institute for Materials Oriented Technologies – IWT is organising an online event next week, on 10.6. 2021, as part of the digital event series ‘Leibniz-IWT live’ with the topic ‘Metal Powder for Additive Manufacturing’. You can register here.
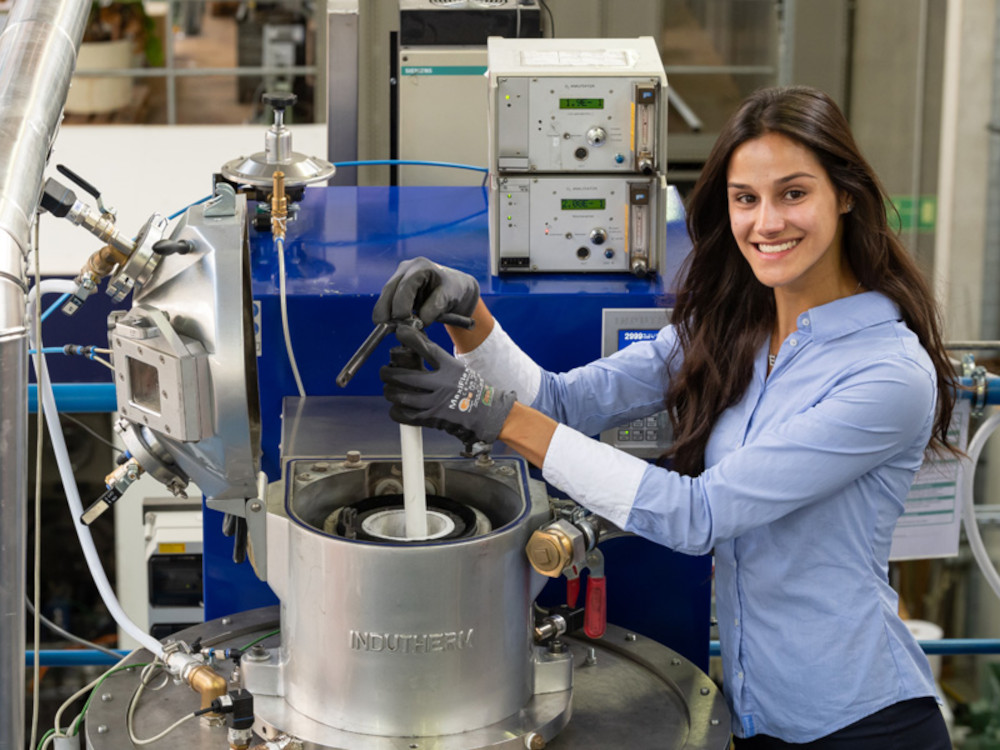
Production of powders for additive manufacturing. Source: Leibniz Institute for Materials Oriented Technologies IWT
Your editorial team of LP.PRO wishes you a relaxing weekend!